Microfabrication techniques — Injection molding
Two types of microfabrication techniques exist:
- Indirect microfabrication method which requires a master with the negative of the design of interest to mold the sign you want on your future microfluidic chip
- Direct microfabrication method which requires no intermediary and directly process the fabric you selected for your future microfluidic chip.
Many techniques (injection molding, hot embossing, polymer ablation,…) can be used for the fabrication of microfluidic chips, but only injection molding technique, which is an indirect microfabrication method, is presented here. The process to obtain the needed intermediary master to produce the chips will not be explained.
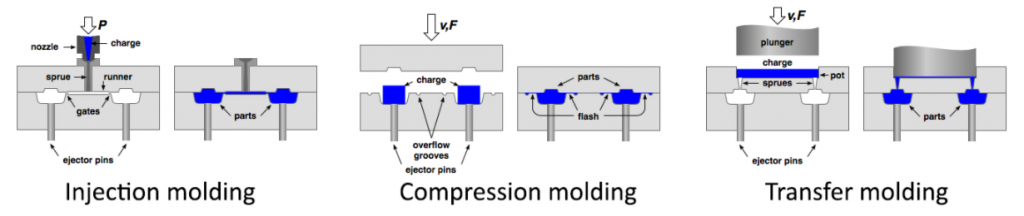
Injection molding [1], [2], [3]
The injection molding process requires the use of a raw plastic material, and a mold. The process consists in 4 steps:
- clamping ー the two parts of the mold have to be securely closed, larger machines will require longer time for this step,
- injection ー the raw plastic material is fed into the machine and is melted by heat and pressure; then, it is quickly injected into the mold,
- cooling ー the molten plastic will naturally cool with the contact of the mold surfaces; the cooling time can be estimated from several thermodynamic properties of the plastic and the maximum wall thickness of the part,
- ejection ー when the substrate is cooled enough, a mechanism is used to push the part out of the mold as during cooling the part shrinks and adheres to the mold.
In order to completely fill the microstructure mold with high aspect ratio, the common injection molding parameters (low tool temperatures, injection pressures) should be changed: above Tg for amorphous thermoplastics, around melting point for semi-crystalline thermoplastics for example.
- Advantages: can form complex shapes and fine details (suitable for highest aspect ratio like those obtained with LIGA masters – 100:1 -), excellent surface finish, good dimensional accuracy, low labor cost, scrap can be recycled, very short process (between 2 seconds and 2 minutes) which induces high production rate.
- Drawbacks: high tooling and equipment cost, long lead time possible.
- Main applications: mass replication.
- Adapted for: thermoplastics but feasible for elastomer and thermosets.
- Structures range: up to very high aspect ratios (100:1).
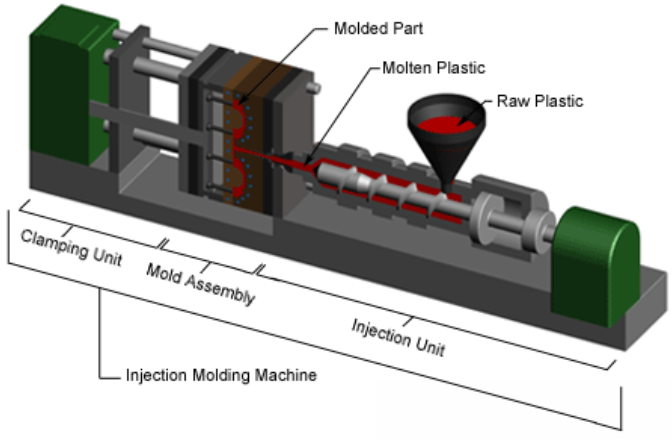
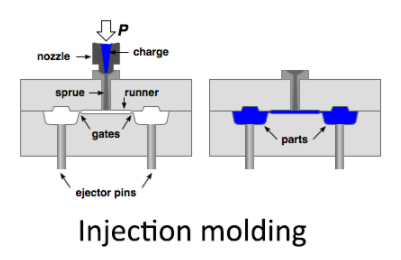
References
[1] R. M. McCormick, R. J. Nelson, M. G. Alonso-Amigo, D. J. Benvegnu, H. H. Hooper, Microchannel electrophoretic separations of DNA in injection-molded plastic substrates. Anal. Chem. 69 (1997) 2626.
[2] V. Piotter, T. Hanemann, R. Ruprecht, J. Haußelt, Injection molding and related techniques for fabrication of microstructures, Microsystem Technologies (1997) 129—133.
For general information
For further information, do not hesitate to contact our team of experts:
contact@blackholelab.com or phone: +33(0).782.831.207