Mold fabrication —Soft lithography
Two types of microfabrication techniques exist:
- Indirect microfabrication method which requires a master with the negative of the design of interest to mold the sign you want on your future microfluidic chip
- Direct microfabrication method which requires no intermediary and directly process the fabric you selected for your future microfluidic chip.
Among indirect microfabrication methods, many have been used in the past for the fabrication of molding tools but not all of them are suitable for microfluidics. Only soft lithography technique is presented here.
Photolithography is an optical means for transferring patterns onto a substrate. It uses light to transfer a geometric pattern from a mask to a light-sensitive chemical photoresist on the substrate and is then developed with a chemical product (developer).
The different parameters for photoresists are: resolution, contrast, sensitivity to light (generation of well-defined structure), sensitivity to development, viscosity, adherence, anti-etching and surface tension [1].
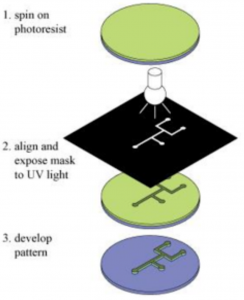
Master fabrication steps (with a negative photoresist) include spin coating of a photoresist film, exposure to UV light (the molecules of the exposed photoresist are crosslinked), and development (uncrosslinked photoresist is removed). Image source: Qi, D., Hoelzle, D.J., Rowat A.C., Probing single cells using flow in microfluidic devices, The European Physical Journal Special Topics, 204, 2012, 87
There are two families of photoresists:
- negative photoresists (e.g.: epoxy based like SU-8)ー the insulated part stays after development, the other regions are dissolved in developer, excellent adhesion to silicon, less expensive than positive ones, organic, minimum feature size of 2µm, excellent wet chemical resistance;
- positive photoresists (e.g.: mixture of diazonaphthoquinone (DNQ) and novolac resin (a phenol formaldehyde resin)) ー the uninsulated part stays after development, the other regions are dissolved in developer; fair adhesion to silicon, more expensive than negative ones, aqueous, minimum feature size of 0.5µm, fair wet chemical resistance.
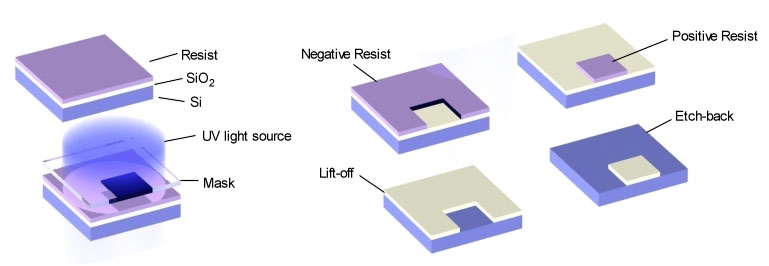
Among those two families, two types of photoresist exist:
- liquid photoresist (e.g.: SU-8, AZ) ー the resist is spincoated onto a substrate to a desired thickness that sets the channel height. These resists require some baking steps in order to harden and be correctly fixed to the substrate.
- dry film (e.g.: Ordyl, Riston) ー the resist can be laminated onto the substrate and adhere with heating. The process might be easier than with liquid photoresist as, for example, Ordyl dry films do not need any baking step to be fixed.
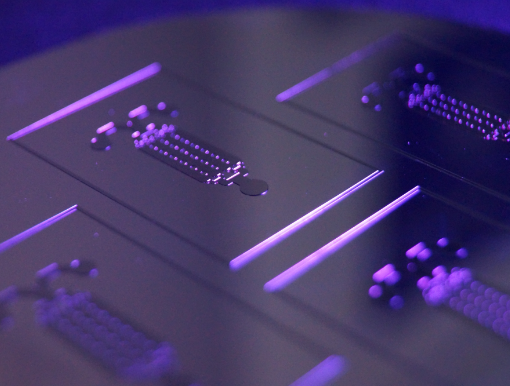
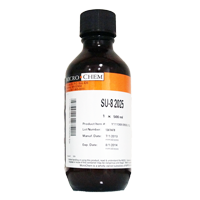
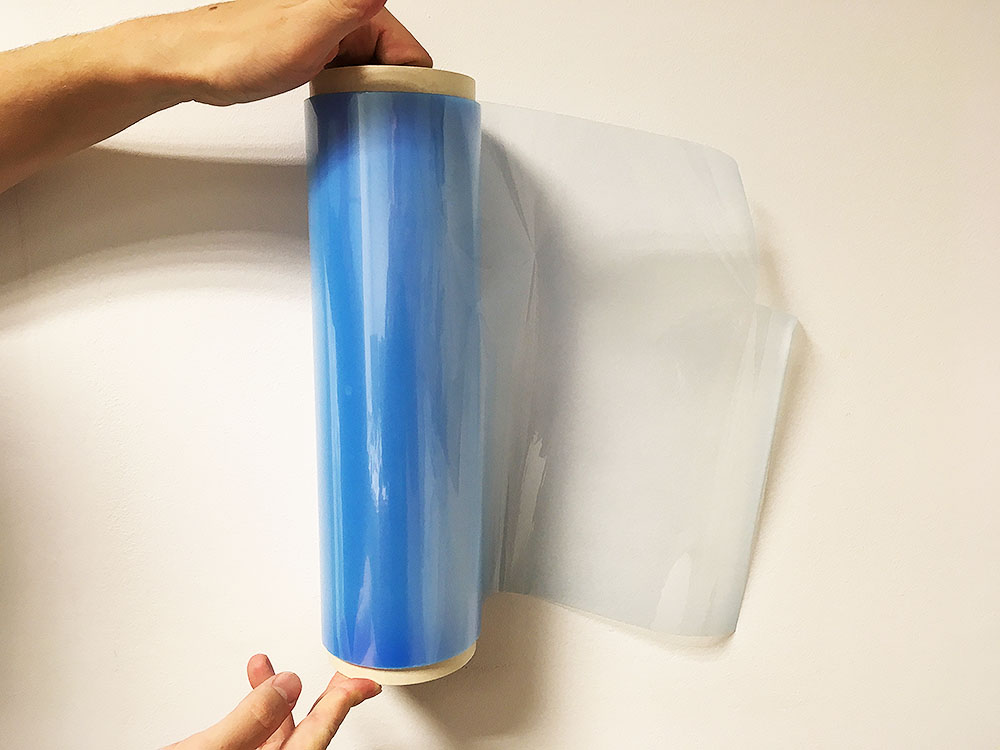
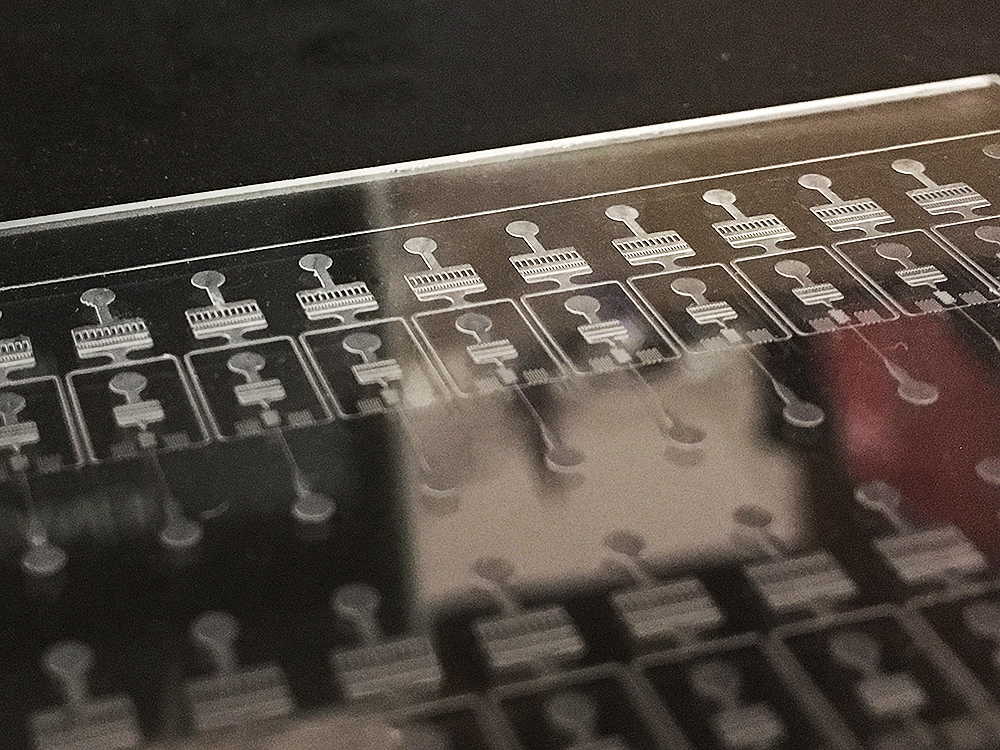
SU-8 is an epoxy-based negative photoresist which is commonly used in microfluidics to create mold. Even though it is more complicated to use than dry film photoresists (spin-coating, multiple land long baking steps,…), SU-8 resin offers a great quality of mold and is very resistant.
BlackHole Lab offers a SU-8 mold fabrication station which enables you to create your mold thanks to SU-8 resist.
The other option is to use dry film photoresists. The process to use these films is more simple than liquid resist procesesses. After cutting a piece of photoresist film, the film needs to be stuck to the support, generally thanks to heating, before being insulated with the wanted design. After simple development, the mold is ready to use without any baking process.
BlackHole Lab offers a Dry film lamination station for soft lithography which is compatible with Ordyl and Riston films. These two films are the only dry films that we have tested in lab. If you have any suggestion, feel free to contact us for any test.
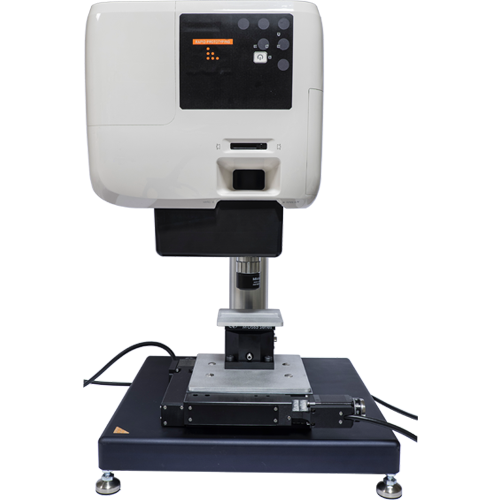
Thus, photolithography is usually a binary pattern transfer due to the use of a mask which is either black (and doesn’t let light go through it) or transparent (and let light go through it). But, some companies try to develop processes and engines that are maskless devices. This enables to insulate photoresist by the projection of the light in the exact shape of the design you need. With this method, we can imagine the possibility to achieve grayscale patterns with different heights of resist.
BlackHole lab offers this type of maskless exposure system for microfabrication with the Smartprint [2] technology.
References
[1] J. J. Greener, W. Li, J. Ren, D. Voicu, V. Pakharenko, T. Tang, E. Kumacheva, Rapid, cost-efficient fabrication of microfluidic reactors in thermoplastic polymers by combining photolithography and hot embossing, 2010, Lab Chip. 10 (4): 522–524.
For general information
For further information, do not hesitate to contact our team of experts:
contact@blackholelab.com or phone: +33(0).782.831.207